Due to production needs, the feed factory needs to add a 4Ton biomass boiler to provide stable heat energy for feed drying. The DZL series of biomass boilers are developed and designed jointly by ZOZEN’S and Shanghai Jiaotong University based on the characteristics and burning rate of various biomass fuels, through numerical simulation, reasonable layout of furnace arches, furnace walls, and furnace heating surfaces. Feed mills will produce a large amount of crop waste residues during production, and ZOZEN’S recommends using these waste residues as fuel for biomass boilers. Compared with traditional boilers, DZL series biomass boilers have a larger furnace space, and at the same time, the arrangement of very reasonable secondary air enables full combustion and effectively reduces NOX emissions. The feed plant steam boiler is equipped with a speed control box, and the speed can be adjusted reasonably according to the biomass burning rate to ensure that the fuel is burned out and achieve zero carbon dioxide emissions.
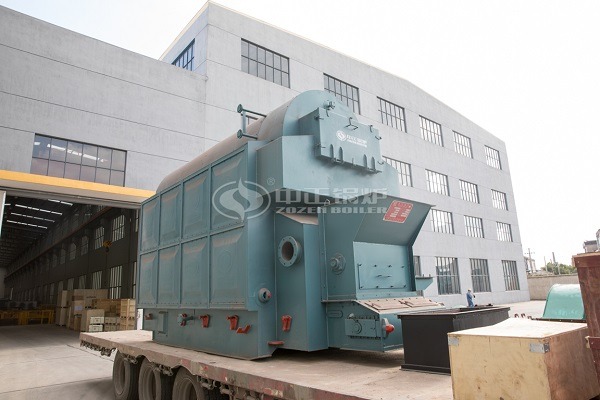
This biomass fired boiler uses crop waste generated from feed as fuel, reducing fuel costs. The boiler has high efficiency, full combustion, and exhaust gas emission in full compliance with national standards. It is a new environmentally friendly product that protects the environment. The feed, combustion, slag removal, water supply and ignition of this series of steam boilers can be automatically controlled, and the operation is very convenient. The boiler is equipped with an automatic ash removal device, which can remove the ash on the heating surface of the boiler in time to ensure the efficient and stable operation of the boiler. An economizer is arranged at the tail of the boiler, and an air preheater can also be arranged according to user needs. Compared with traditional boilers, the boiler has higher efficiency and lower exhaust gas temperature.
The feed plant steam boiler is produced in strict accordance with the specifications and standards, and all the pressure parts are made of high-quality boiler steel. Each boiler must undergo rigorous inspection and testing before leaving the factory, including water pressure test and X-ray inspection. There are manholes, inspection doors, fire viewing holes, etc., which are very convenient for maintenance. The biggest feature of biomass fired boiler is: energy saving, environmental protection, and easy to install and use.
DZL series biomass boiler has strong fuel adaptability, high boiler thermal efficiency, good environmental protection performance, sufficient boiler output, and convenient use and maintenance. This series of boilers product overall structure adopts a new-type steam boiler with a single drum vertical arrangement. There are water-cooled walls on both sides of the furnace. The upper end is welded to the drum, and the lower end is welded to the left and right headers. The space between the back arch and the drum is arranged with a convection tube bundle. The upper end of the tube bundle is welded to the drum and the lower end is welded to the headers. The structure is very compact. In the product design of the boiler, the furnace is designed into two parts: a combustion chamber and a combustion chamber, which is beneficial to strengthen the combustion of fuel in the combustion chamber, and is beneficial to reduce the content of fly ash combustibles and fly ash.
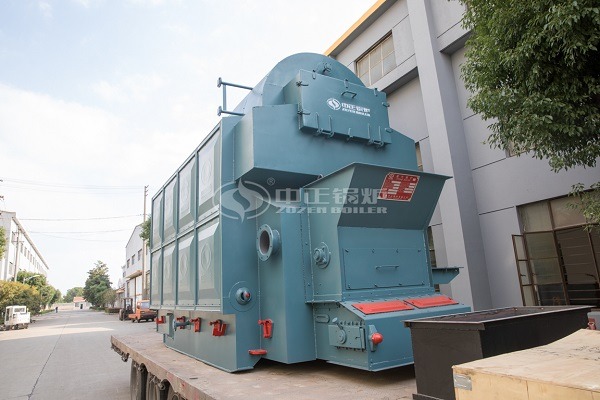
The convection tube bundle of the feed plant steam boiler makes the flue gas return many times, which is beneficial to the dust removal in the furnace. The biomass steam boiler uses a reasonable boiler structure to support its own weight without a steel frame. The use of energy-saving and strong radiation furnace arch can achieve stable combustion of fuel. At the same time, high-standard, high-quality auxiliary machinery, accessories and automatic control equipment are used, and the boiler operates stably, and at the same time reduces the labor intensity of the furnace workers.