The optimized utilization of the heating area of the heavy oil steam boiler is based on the principle that the heat exchange in the furnace is proportional to the fourth power of the temperature. The furnace has a large furnace shell space, a large effective radiant heating surface, and a large proportion of the furnace radiant heat absorption in the total heat absorption. The air distribution in the heavy oil boiler manufacturing furnace is uniform, and the temperature field in the furnace is extremely uniform. Especially when the corrugated furnace is installed near the flame center, the convective heat transfer becomes stronger. The smoke tube bundle is a two-pass, low-flow design, which effectively reduces the smoke and wind resistance of the body, and can significantly reduce the operating power consumption of the blower, and the boiler does not require an induced draft fan.
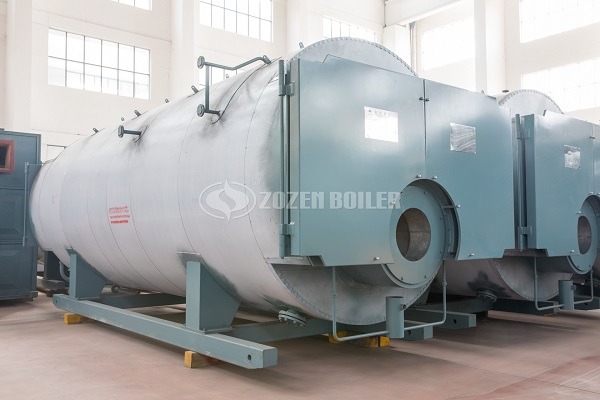
This series of steam boilers has less heat loss and can obtain higher thermal efficiency than other structures. Compared with the dry back type, there is no heat dissipation from the rear smoke box cover. This type of oil-fired boiler adopts a downstream full-wet back structure, and the flue gas inlet temperature to the tube sheet is lower than 1000 ℃, which can avoid the phenomenon of super-cooled boiling on the inner wall of the tube sheet and the rapid formation of scale, which greatly improves the front of the back-combustion chamber. The working conditions of the tube sheet can reduce the cracking accident of the tube sheet. The boiler furnace liner adopts a corrugated furnace liner structure, which not only increases the radiation and convection heat transfer area, but also meets the need for the furnace liner to expand freely after high temperature radiation.
The heavy oil steam boiler has low flue gas flow resistance and low operating power consumption, which can save operating costs. The convection tube bundle of the boiler adopts a new type of heat transfer element-threaded tube, which greatly enhances the heat transfer, thereby reducing the convection heating area and reducing the cost of the boiler. The welding of the heavy oil boiler manufacturing furnace and the front and rear tube plates adopts the flange butt connection to ensure the welding quality. The smoke box of this series of boiler products adopts double-opening smoke box door, open lunch, multi-stage labyrinth seal, seal raw materials, good compressibility, block the leakage of smoke, and can be reused.
The operating parameters of a 10ton oil-fired steam boiler under rated load are: the feed water temperature is 20°C, the pressure is 1.25MPa, and 10 tons of water vapor with a temperature of 194°C can be produced within 1 hour. When heavy oil is used as fuel, the calculated thermal efficiency is 96.3%, the exhaust gas temperature is 72℃, and the light oil consumption is 780kg/h. When this series of steam boilers are in operation, the fuel is ejected from the burner, ignited by the electronic ignition rod, and burned in the furnace with slight positive pressure. The high-temperature flue gas turns 180° from the back-combustion chamber into the second and third-pass threaded smoke pipes, turns 180° from the upper part of the rear smoke box, enters the economizer for heat exchange, and is discharged into the atmosphere through the chimney.
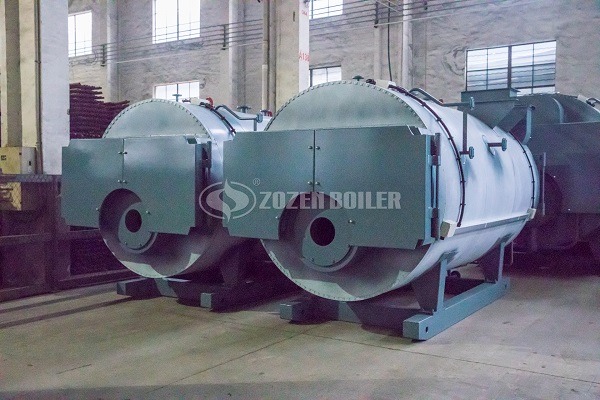
The working fluid of the heavy oil boiler manufacturing is heated to produce saturated steam and output from the main steam valve to the operating system. If the smoke and dust are generated due to improper air adjustment, they can settle in the front and rear smoke boxes and burnout chambers respectively, and all can be cleaned by opening the inspection door. The entire heating surface of this series of boilers is arranged symmetrically, the structure is strong, and the water circulation system is reasonable. The upper drum of the WNS series steam boiler has large water capacity, large steam space, good steam quality, and small water level fluctuations during operation. The distance between the two drums is large, and the pipe diameter is large to ensure good natural circulation. The unique furnace setting and the way of flushing the hot surface by the flue gas make the heat dissipation loss of the boiler small.