The pipes of gas-fired thermal oil boilers should also be cleaned regularly to prevent coking or blockage. Insufficient heat conduction will directly affect the quality of the product. If the boiler is not cleaned, it will cause pollution to the new oil, which will affect the quality of the oil and shorten its service life. Therefore, the coking and fouling of gas-fired thermal oil boilers should be cleaned up regularly. The gas thermal oil boiler work high efficiency, and the working process is essentially a process of energy conversion and transfer in the boiler.
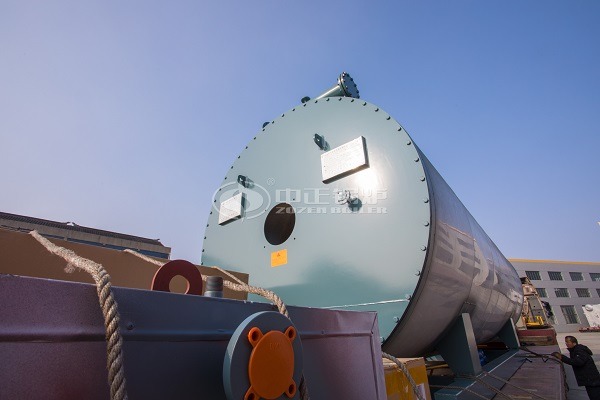
And if we want to extend the service life of the gas-fired thermal oil boiler, in addition to purchasing the boiler from a regular manufacturer, we must also choose a boiler that suits our actual needs. The when installing a gas-fired thermal oil boiler, we must also look for A formal and qualified company to install and debug the gas-fired thermal oil boiler. The working process of a thermal oil boiler in normal operation should include three simultaneous, coordinated, stable and continuous energy conversion and transfer processes in the furnace, heat transfer, and boiler. For the smooth progress of these three processes, thermal oil boilers usually need to control and adjust these three aspects. The thermal oil boiler is to control and adjust the fuel, air and smoke, and thermal oil, and to maintain and manage the corresponding equipment.
The gas thermal oil boiler work heat transfer process of refers to the heat exchange process in which the heat of the high-temperature flame and flue gas is transferred to the heated medium through the “heating surface”. The in-furnace process of this series of boiler products refers to the organization of reasonable and sufficient combustion of the fuel in the furnace. So that the chemical energy of the fuel is fully released in the form of heat energy in the furnace process, so that the flame and flue gas have a high-temperature exothermic process. The process in the pot refers to the process in which the temperature of the medium rises after being heated, heat transfer occurs, and the state changes, and then it is output in the form of heat transfer oil. The medium in this process absorbs heat and changes its state.
YYQW series boiler body heating surface structure is compact. The heating surface is composed of inner and outer densely arranged disks. The inner coil is a radiation heating surface, and the outer coil and the outer surface of the inner coil form a convection heating surface. The boiler is composed of the upper body and the lower combustion chamber. At the same time, the boiler design makes installation more convenient and fast. The boiler adopts intelligent control to make the boiler operation especially convenient and simple. The controller has the functions of automatic ignition and shutdown program control, automatic combustion control, automatic switch and control of circulating pump, automatic fault processing and alarm, etc.
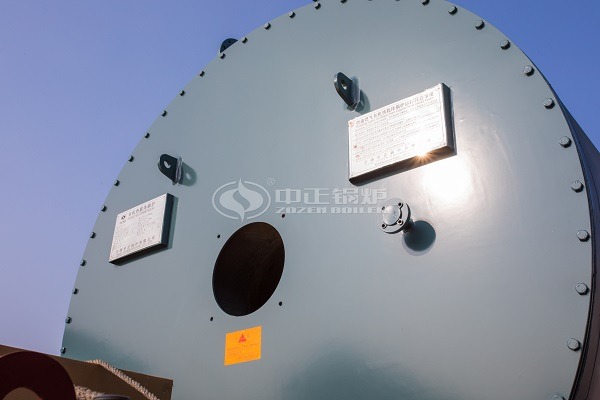
The gas thermal oil boiler work has high thermal efficiency, stable operation and long service life. The gas-fired thermal oil boiler manufacturer tells everyone that the heat-conducting oil is easy to oxidize during heating. As the acid value of the oil increases, the kinematic viscosity will gradually increase. The heat transfer oil can transfer heat energy, which will cause the gel-like inner wall to appear adhesion effect. This makes it easy to form coke. In addition, if air enters, the air and hot oil are likely to polymerize and form coking. The heat transfer oil whose working temperature exceeds the design temperature, as well as the contamination of corrosion products and impurities, will cause the inner wall of the tube to form coking. Therefore, we must clean the gas-fired thermal oil boiler regularly after use to avoid damage to the machine.